INS selected for certifiable train localization project (CLUG)
SBG INS/GNSS selected for certifiable train localisation project (CLUG) led by major European railway companies.
“SBG Systems provides excellent inertial sensors. It was important for us to work with a reliable, local provider.” | Valentin B. – Train Localization Project Manager at SNCF
With the digitalization of transport services, train localization in real-time has become increasingly important for the European railway sector and European travelers.
Currently, the position of the train for signaling purposes is based on trackside equipment such as track circuits or axle counters, which are mounted devices at specific intervals along the railway track. Using GNSS could prove to be a game-changer for the European railway network.
What’s the CLUG Project?
The CLUG project means “Certifiable Localization Unit with GNSS“.
It’s a 2-year project (starting January 2020) gathering a large and complete consortium of different partners comprising railway companies (SNCF, DB NETZ, and SBB), railway signaling industries (CAF and Siemens), navigation specialists (Airbus Defense and Space, Naventik, FDC), a research institute (ENAC), and a certification expert (Navcert).
It builds on the use of GNSS coupled with other sensors (such as IMU and odometer) to provide a continuous and accurate train localization that could be integrated into the future European Rail Traffic Management System (ERTMS).
The EU-funded CLUG project will assess the creation of a failsafe on-board localization unit, with the 4 following characteristics:
– A failsafe on-board multi-sensor localization unit consisting of a navigation core (IMU, tachometer, etc.) brought in reference using GNSS, track map, and a minimal number of reference points;
– An on-board continuous localization system that provides location, speed, and other dynamics of the train;
– Operational and interoperable across the entire European rail network;
– It will be compatible with the current ERTMS TSI or with its future evolutions.
Why could it be a Game-Changer for the European Railway Network?
By enabling a significant reduction of trackside equipment – also meaning less fragile and vulnerable equipment – and improving localization performance, the CLUG project could prove to be a game-changer for the European railway network.
Ultimately, this project is the key enabling technology for the future-proof development of train digitalization and automation.
Efficiency, punctuality, and safety: this future train technology will respond to the increased mobility needs of all European travelers and offer them an improved customer experience.
Certifiable train localisation project (CLUG) led by major European railway companies
Two different inertial navigation systems have been selected for the CLUG project experimentations. “SBG Systems provides excellent inertial sensors; it was important for us to work with a reliable, local provider,” indicates Valentin Barreau, Train Localization Project Manager at SNCF.
First, the Apogee-D is an all-in-one inertial navigation system integrating a tri-frequency GNSS receiver providing a very high-accuracy attitude (0.008°), true heading (0.015°), and position.
The second INS is the Ekinox-E, an externally-aided inertial navigation system, which can be connected to an external GNSS receiver chosen by the user.
It delivers an attitude up to 0.02° in real-time and is coupled here with a GNSS receiver for true heading (0.05°) and continuous position in case of GNSS outages.
The CLUG team also connects an odometer to both INS for even higher performance, especially in long tunnels. For this particular application, CLUG uses INS raw data. Airbus Defense and Space designed the algorithm used to generate the train localization, and employs the Apogee inertial and GNSS data post-processed as a reference for the testing phase.
Like all SBG inertial sensors, Apogee-D and Ekinox-E benefit from an extensive testing, screening, and calibration process.
Each sensor is individually calibrated from -40°C to 85°C and is shipped with its calibration report. Sensors are tested, and only those that meet specifications are delivered. This process ensures the highest level of reliability.
SBG Systems’ INS used in train localisation
Apogee and Ekinox INS provide real-time fused data but also enables post-processing thanks to an integrated data logger.
Post-processing is made easy with SBG’ in-house PPK software called Qinertia. Qinertia offers a unique VBS feature that automatically includes multiple publicly available sources of corrections in the post-processed solution.
Thus, VBS transforms the corridor mapping operations of hundreds of kms of railways into a seamless task.
Results of this amazing experimentation are expected in December 2021. Follow every step of this technical adventure on the CLUG website and Social Networks.
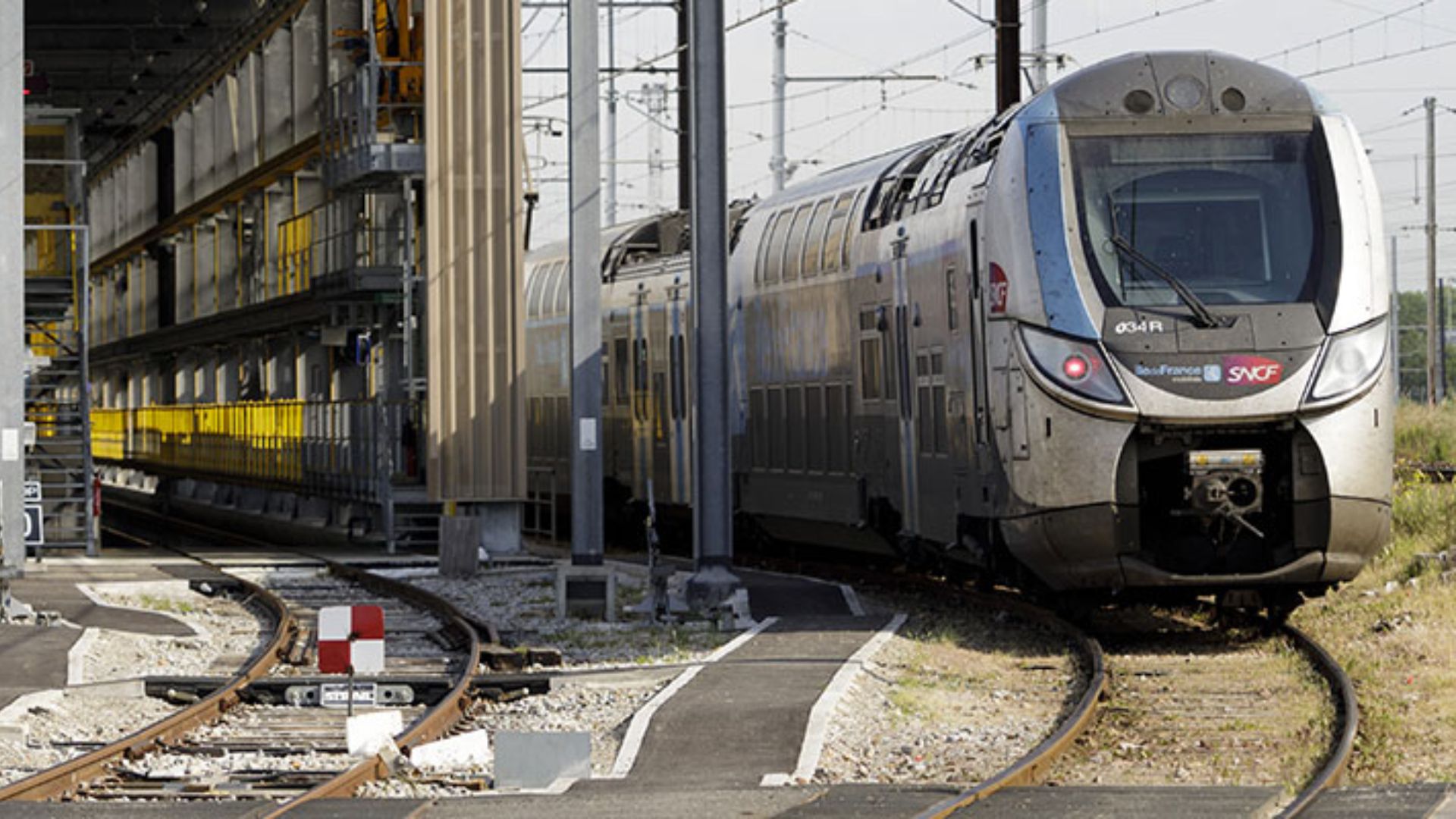
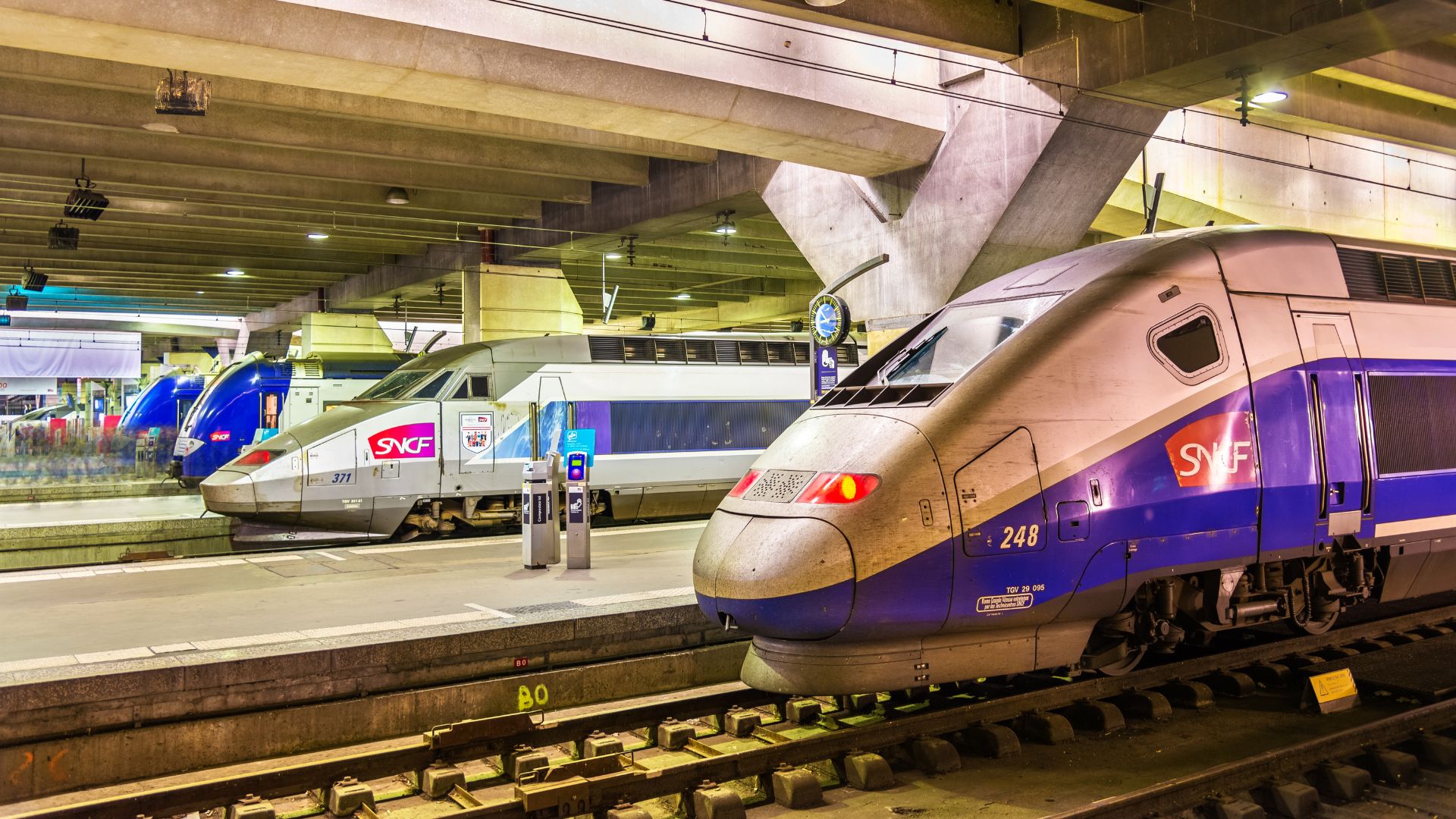
Apogee-D
Ellipse-D is an inertial navigation system integrating a dual antenna and dual frequency RTK GNSS that is compatible with our Post-Processing software Qinertia.
Designed for robotic and geospatial applications, it can fuse Odometer input with Pulse or CAN OBDII for enhanced dead-reckoning accuracy.
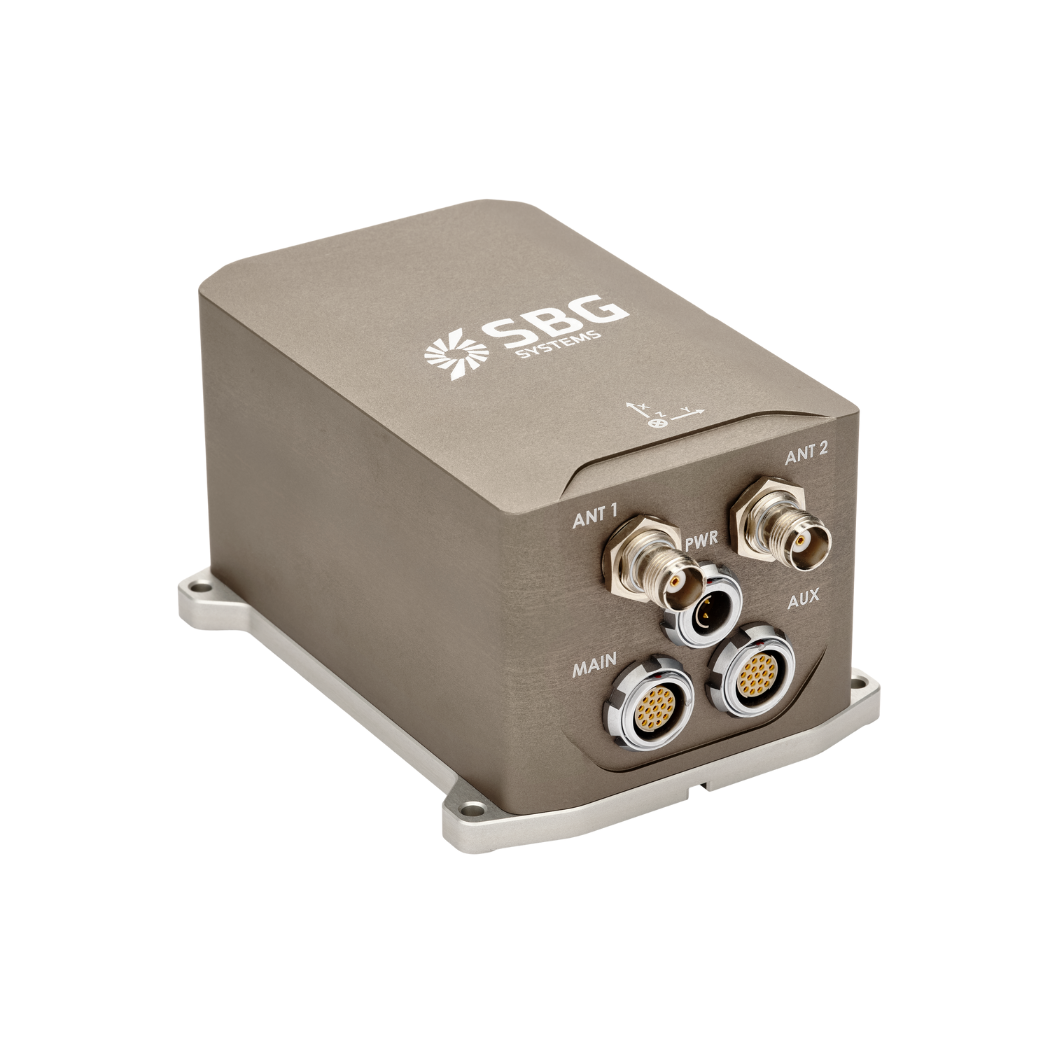
Ask a quotation for Apogee-D
Do you have questions?
Welcome to our FAQ section! Here, you’ll find answers to the most common questions about the applications we showcase. If you don’t find what you’re looking for, feel free to contact us directly!
What is GNSS vs GPS?
GNSS stands for Global Navigation Satellite System and GPS for Global Positioning System. These terms are often used interchangeably, but they refer to different concepts within satellite-based navigation systems.
GNSS is a collective term for all satellite navigation systems, while GPS refers specifically to the U.S. system. It includes multiple systems that provide more comprehensive global coverage, while GPS is just one of those systems.
You get improved accuracy and reliability with GNSS, by integrating data from multiple systems, whereas GPS alone might have limitations depending on satellite availability and environmental conditions.
What is GNSS post-processing?
GNSS post-processing, or PPK, is an approach where the raw GNSS data measurements logged on a GNSS receiver are processed after the data acquisition activity. They can be combined with other sources of GNSS measurements to provide the most complete and accurate kinematic trajectory for that GNSS receiver, even in the most challenging environments.
These other sources can be local GNSS base station at or near the data acquisition project, or existing continuously operating reference stations (CORS) typically offered by governmental agencies and/or commercial CORS network providers.
A Post-Processing Kinematic (PPK) software can make use of freely available GNSS satellite orbit and clock information, to help further improve the accuracy. PPK allow for precise determination of a local GNSS base station’s location in an absolute global coordinate reference frame datum, which is used.
PPK software can also support complex transformations between different coordinate reference frames in support of engineering projects.
In other words, it gives access to corrections, enhances the project’s accuracy, and can even repair data losses or errors during the survey or installation after the mission.
What is the difference between IMU and INS?
The difference between an Inertial Measurement Unit (IMU) and an Inertial Navigation System (INS) lies in their functionality and complexity.
An IMU (inertial measuring unit) provides raw data on the vehicle’s linear acceleration and angular velocity, measured by accelerometers and gyroscopes. It supplies information on roll, pitch, yaw, and motion, but does not compute position or navigation data. The IMU is specifically designed to relay essential data about movement and orientation for external processing to determine position or velocity.
On the other hand, an INS (inertial navigation system) combines IMU data with advanced algorithms to calculate a vehicle’s position, velocity, and orientation over time. It incorporates navigation algorithms like Kalman filtering for sensor fusion and integration. An INS supplies real-time navigation data, including position, velocity, and orientation, without relying on external positioning systems like GNSS.
This navigation system is typically utilized in applications that require comprehensive navigation solutions, particularly in GNSS-denied environments, such as military UAVs, ships, and submarines.
What is the difference between RTK and PPK?
Real-Time Kinematic (RTK) is a positioning technique where GNSS corrections are transmitted in near real time, typically using an RTCM format correction stream. However, there can be challenges in ensuring the GNSS corrections, specifically their completeness, availability, coverage, and compatibility.
The major advantage of PPK over RTK post processing is that the data processing activities can be optimized during post-processing, including forward and backward processing, whereas in real-time processing, any interruption or incompatibility in the corrections and their transmission will lead to lower accuracy positioning.
A first key advantage of GNSS post-processing (PPK) vs. real time (RTK) is that the system used on the field does not need to have a datalink/radio to feed the RTCM corrections coming from the CORS into the INS/GNSS system.
The main limitation to post processing adoption is the requirement of the final application to act on the environment. On the other hand, if your application can withstand the additional processing time needed to produce an optimized trajectory, it will greatly improve the data quality for all your deliverables.